Folding carton applications
From the simple folding box to the complex six-pack
You can rely on it
Folding cartons are getting more complex all the time and no wonder, considering they have to support high-quality product presentation, protect what’s inside, serve as carriers and be as sustainable as possible. These multiple functions put growing demands on gluing and quality assurance systems. With its modular components, Baumer hhs offers a sophisticated and powerful system that meets even the highest of these technical demands: It is the industry benchmark.
Your applications Our solutions
Baumer hhs is your Partner
Our systems can be adapted to your individual needs. Benefit from our technology lead and Baumer hhs’s reputation for reliability.
Modularly designed for configuring complete gluing systems
Easily integrated in existing folder-gluers
OEM supplier to leading packaging machine manufacturers
Future-oriented and economical
For sustainable production
Everything from a single source
We make your team fit for tomorrow
Baumer hhs puts no limits on the possibilities open to its customers.
No matter what kind of products you have in mind, the systems from Baumer hhs for manufacturing folding cartons support a reliable process, even with the most complex products – and even at the highest required machine speeds.
Straight-line boxes
The straight-line box is the most common product in the folding carton industry. In most cases, high volumes of these boxes are produced at maximum machine speed. With Baumer hhs, you can rely on end-to-end monitoring of your production process. Product mix-ups and incorrectly glued joints are reliably identified and ejected.
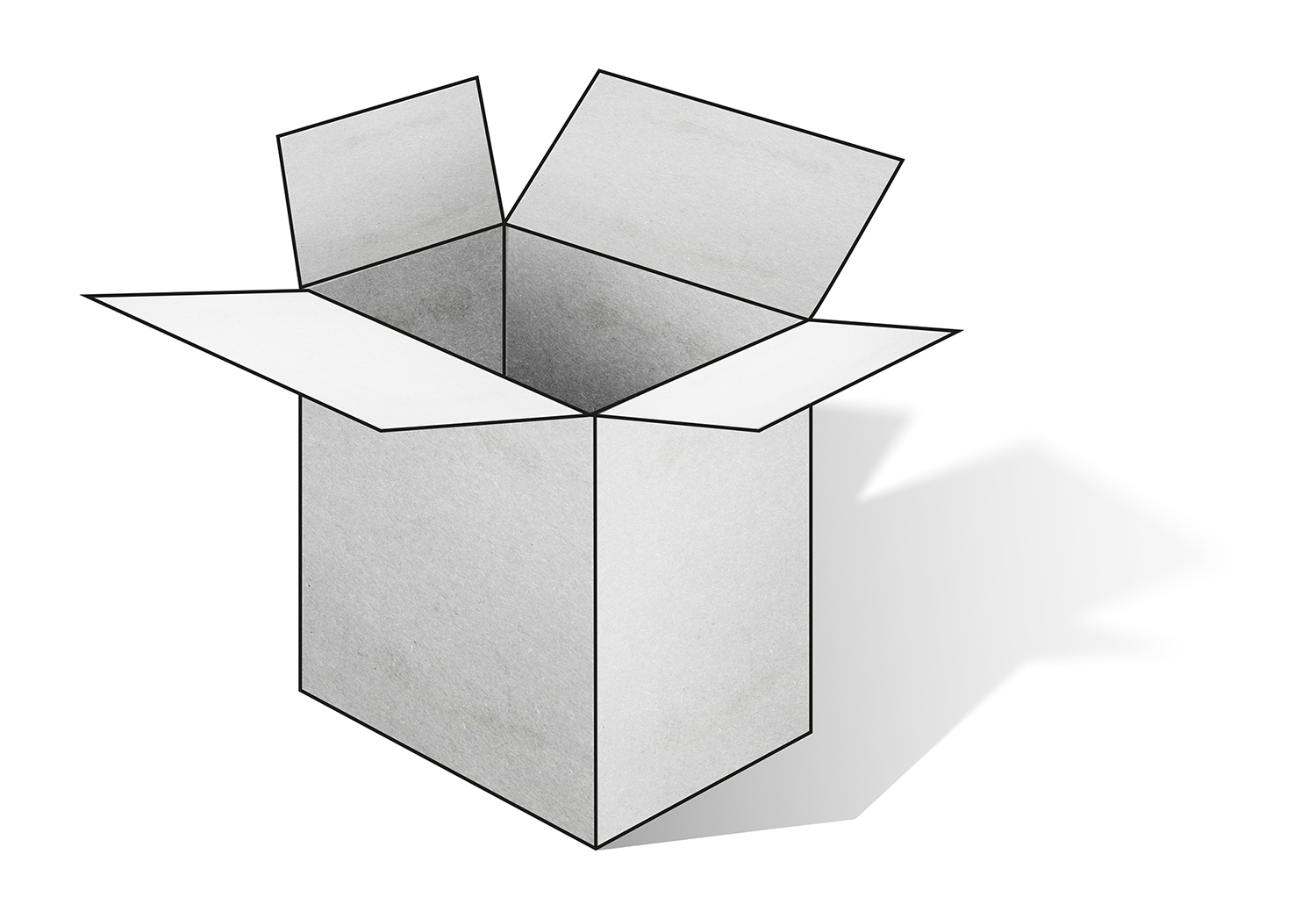
The CT 300 verifies standard colour codes and compact pharmaceutical codes!
- 100% verification to prevent product mix-ups
- Ensures maximum process reliability in folding carton production
- High optical resolution
- Reduces code mark width by 50%
- Capable of monitoring colour on code marks measuring just 0.5mm
LNT 300 – Monitors the application of adhesive coatings using microwave technology!
- Monitors the volume applied across the entire glue flap
- Monitors product length using an integrated light barrier function
- Easy to operate while offering 100% process reliability in production
Product tracking through the machine and ejector control with the T&E module
- 100% process reliability in production - functions on the fail-safe principle
- Continuous production with maximum reliability
- Capable of controlling all common ejector types on the market
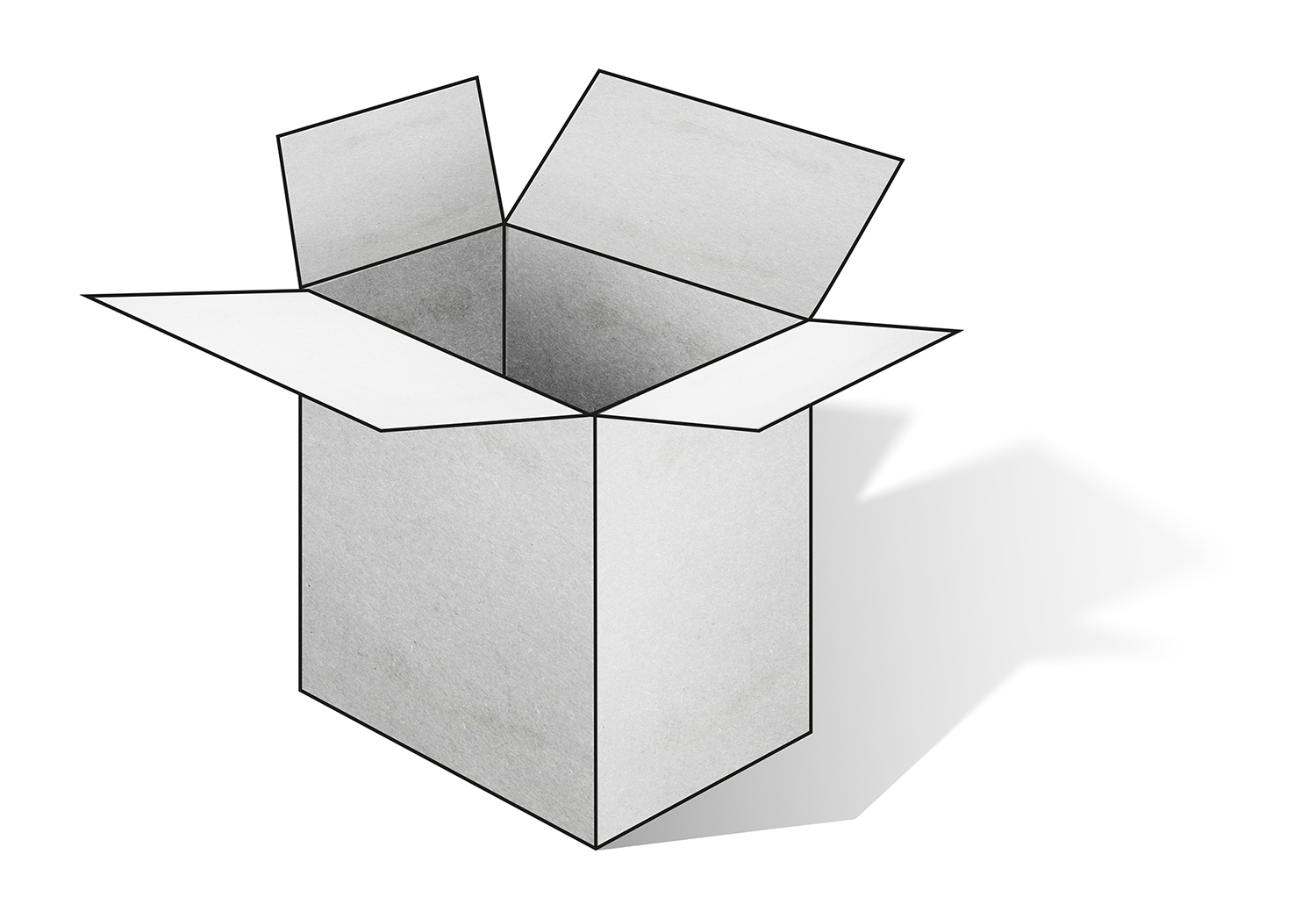
The CT 300 verifies standard colour codes and compact pharmaceutical codes!
- 100% verification to prevent product mix-ups
- Ensures maximum process reliability in folding carton production
- High optical resolution
- Reduces code mark width by 50%
- Capable of monitoring colour on code marks measuring just 0.5mm
LNT 300 – Monitors the application of adhesive coatings using microwave technology!
- Monitors the volume applied across the entire glue flap
- Monitors product length using an integrated light barrier function
- Easy to operate while offering 100% process reliability in production
Product tracking through the machine and ejector control with the T&E module
- 100% process reliability in production - functions on the fail-safe principle
- Continuous production with maximum reliability
- Capable of controlling all common ejector types on the market
Zur Anzeige des Klick-Modells nutzen Sie gerne unsere Desktop-Version.
Crash-lock bottom boxes with
hot melt and cold glue
Folding carton-style premium packaging with sophisticated finishes. Precision gluing on the bottom flap prevents inside gluing, eliminating problems erecting the boxes in the packaging line before they occur.
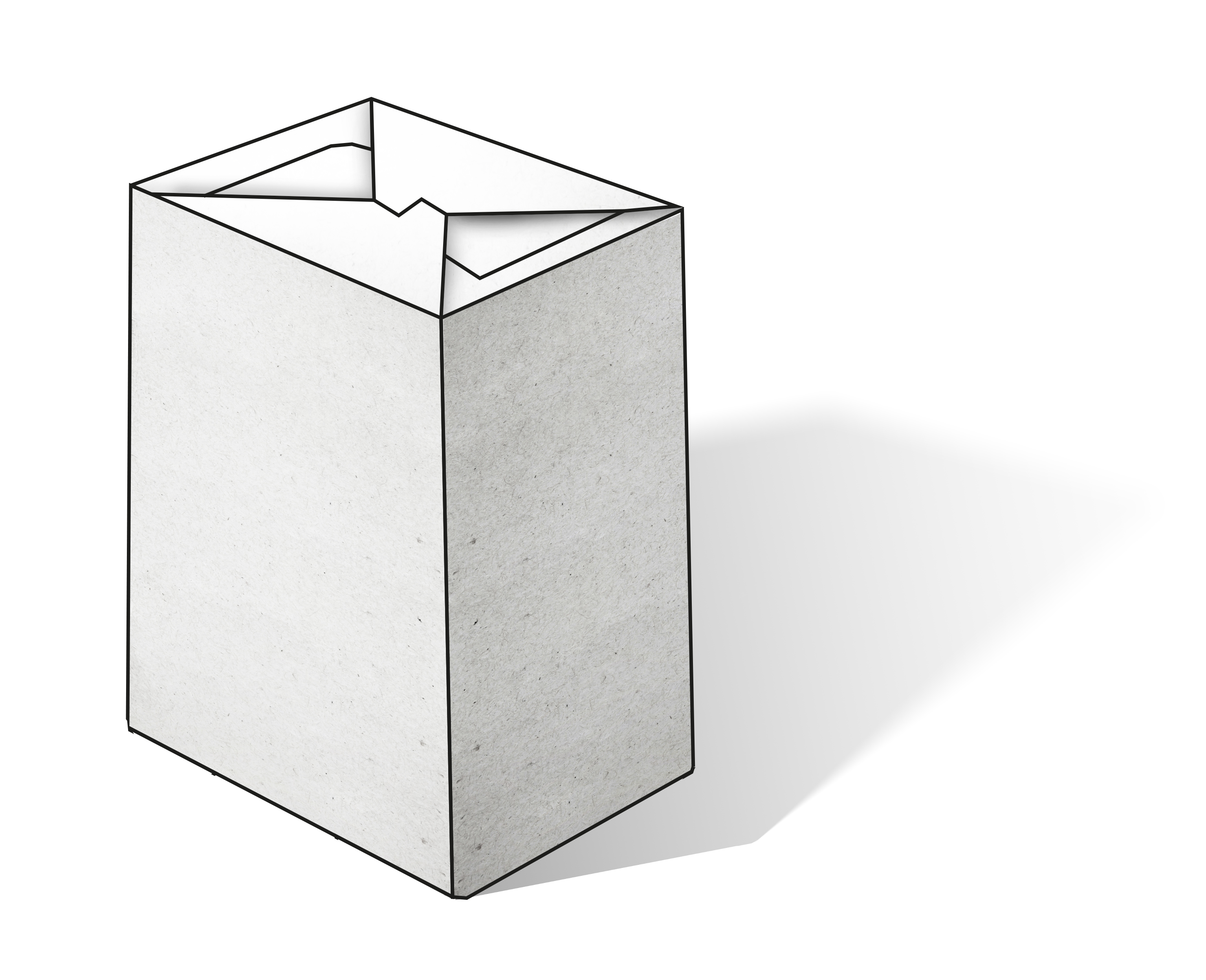
LNT 300 – Monitors the application of adhesive coatings using microwave technology!
- Monitors the volume applied across the entire glue flap
- Monitors product length using an integrated light barrier function
- Easy to operate while offering 100% process reliability in production
Xcam – Monitors adhesive application and diagonal creasing!
Line scan cameras combined with UV or white LED linear lighting.
- Monitors adhesive application
- Detects glue-free areas
- Detects flaps
- Verifies creasing of the bottom flaps
PX 1000 – The application head for precision gluing at maximum production speed!
- High closing force for minimal tailing and precision restart
- Reduced contamination means longer cleaning intervals and maximum productivity
- Processes a wide range of adhesive viscosities
- Maximum service life
- High process reliability in production
GDX 1000 – The optical sensor for monitoring glue application at maximum production speed!
- Monitors glue application 100%
- Monitors glue-free areas
- Integrated light barrier function for monitoring product length
- Sensor can be set up at the Xtend³ controller
The CT 300 verifies standard colour codes and compact pharmaceutical codes!
- 100% verification to prevent product mix-ups
- Ensures maximum process reliability in folding carton production
- High optical resolution
- Reduces code mark width by 50%
- Capable of monitoring colour on code marks measuring just 0.5mm
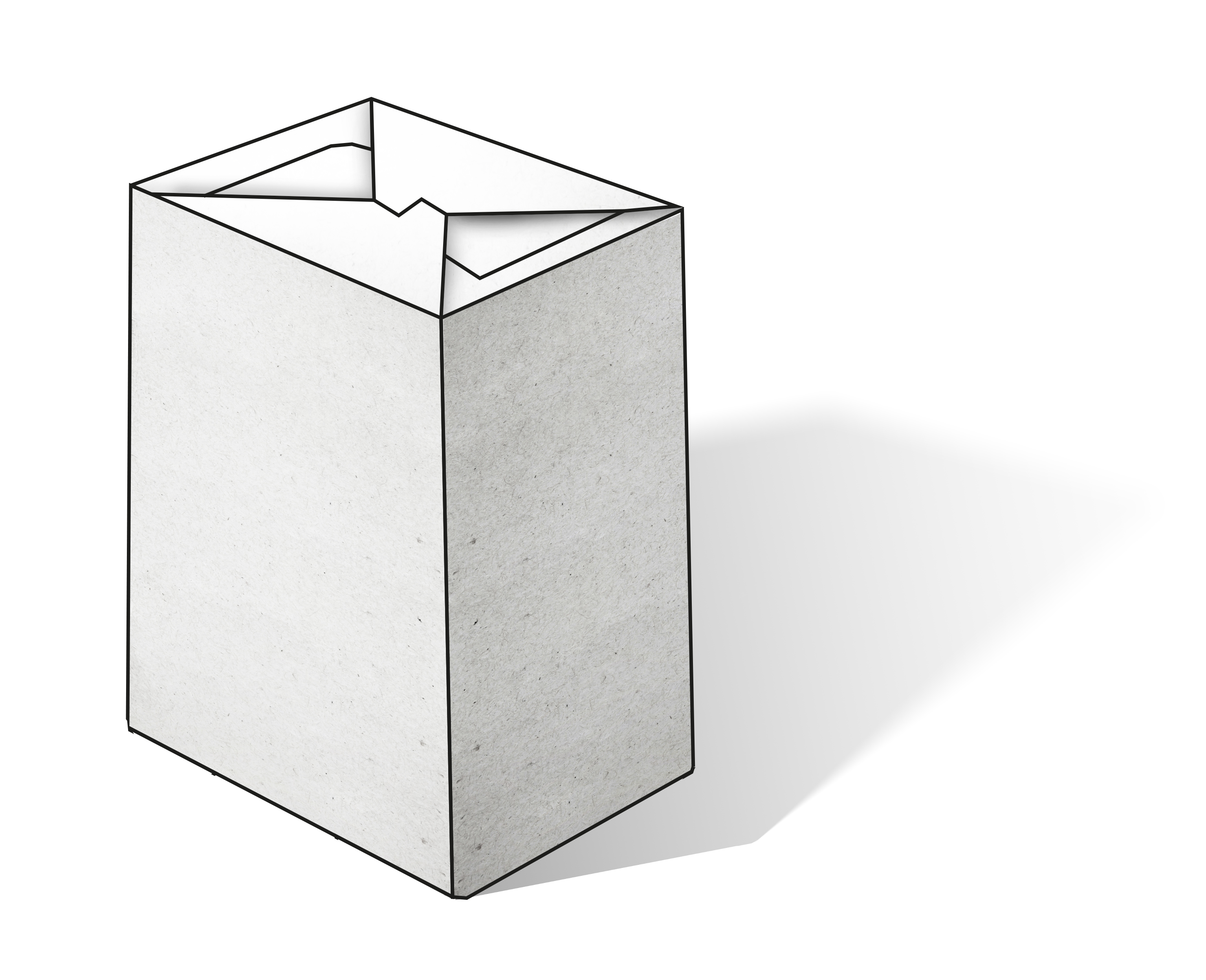
LNT 300 – Monitors the application of adhesive coatings using microwave technology!
- Monitors the volume applied across the entire glue flap
- Monitors product length using an integrated light barrier function
- Easy to operate while offering 100% process reliability in production
Xcam – Monitors adhesive application and diagonal creasing!
Line scan cameras combined with UV or white LED linear lighting.
- Monitors adhesive application
- Detects glue-free areas
- Detects flaps
- Verifies creasing of the bottom flaps
PX 1000 – The application head for precision gluing at maximum production speed!
- High closing force for minimal tailing and precision restart
- Reduced contamination means longer cleaning intervals and maximum productivity
- Processes a wide range of adhesive viscosities
- Maximum service life
- High process reliability in production
GDX 1000 – The optical sensor for monitoring glue application at maximum production speed!
- Monitors glue application 100%
- Monitors glue-free areas
- Integrated light barrier function for monitoring product length
- Sensor can be set up at the Xtend³ controller
The CT 300 verifies standard colour codes and compact pharmaceutical codes!
- 100% verification to prevent product mix-ups
- Ensures maximum process reliability in folding carton production
- High optical resolution
- Reduces code mark width by 50%
- Capable of monitoring colour on code marks measuring just 0.5mm
Zur Anzeige des Klick-Modells nutzen Sie gerne unsere Desktop-Version.
4- and 6-corner folding cartons
These popular folding cartons for food and consumer products, such as baked goods, sweets, fruit and vegetables, are precision-manufactured at high speed. The glue must be applied with maximum precision even on small flaps. The Xcam verifies that all flaps are precisely folded.
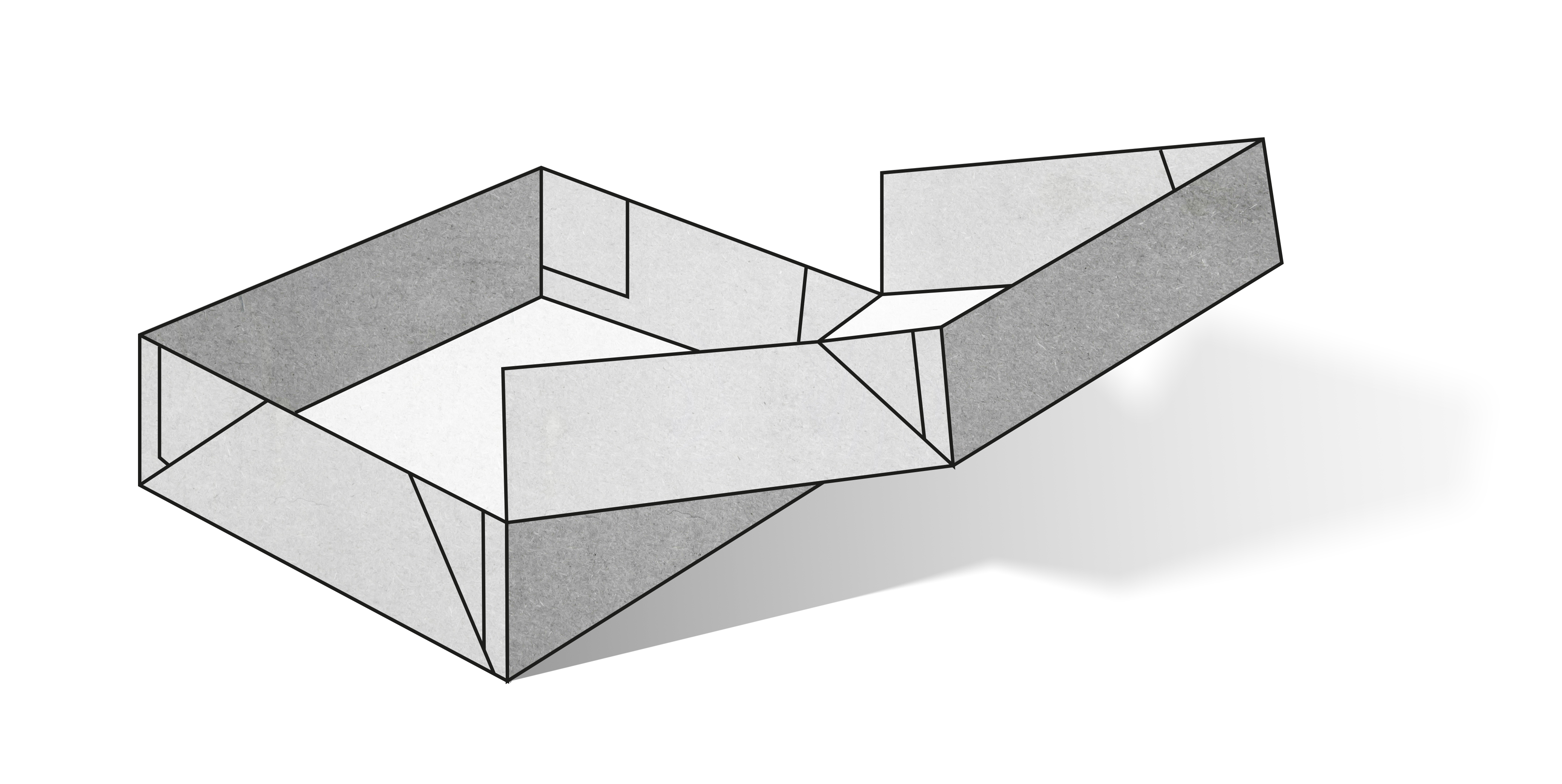
The CT 300 verifies standard colour codes and compact pharmaceutical codes!
- 100% verification to prevent product mix-ups
- Ensures maximum process reliability in folding carton production
- High optical resolution makes it possible to reduce code mark width by 50%
- Capable of monitoring colour on code marks measuring just 0.5mm
PX 1000 – The application head for precision gluing at maximum production speed!
- High closing force for minimal tailing and precision restart
- Reduced contamination means longer cleaning intervals and maximum productivity
- Processes a wide range of adhesive viscosities
- Maximum service life
- High process reliability in production
GDX 1000 – The optical sensor for monitoring glue nozzle application at maximum production speed!
- Monitors glue application 100%
- Monitors glue-free areas
- Integrated light barrier function for monitoring product length
- Sensor can be set up on the screen of the Xtend³ controller
Xcam – Monitors adhesive application and diagonal creasing!
Line scan cameras combined with UV or white LED linear lighting.
- Monitors adhesive application
- Detects glue-free areas
- Detects flaps
- Verifies diagonal creasing of the bottom flaps
The T&E module tracks products through the machine and automatically ejects them!
- 100% process reliability in production - functions on the fail-safe principle
- Ensures continuous production flows and maximum process reliability
- Capable of controlling all ejector types
Scan 300 – Laser scanner for detecting all common EAN codes!
- Examples: Code 128 / 2/5 Interleaved / Code 39
- 100% production control to prevent product mix-ups
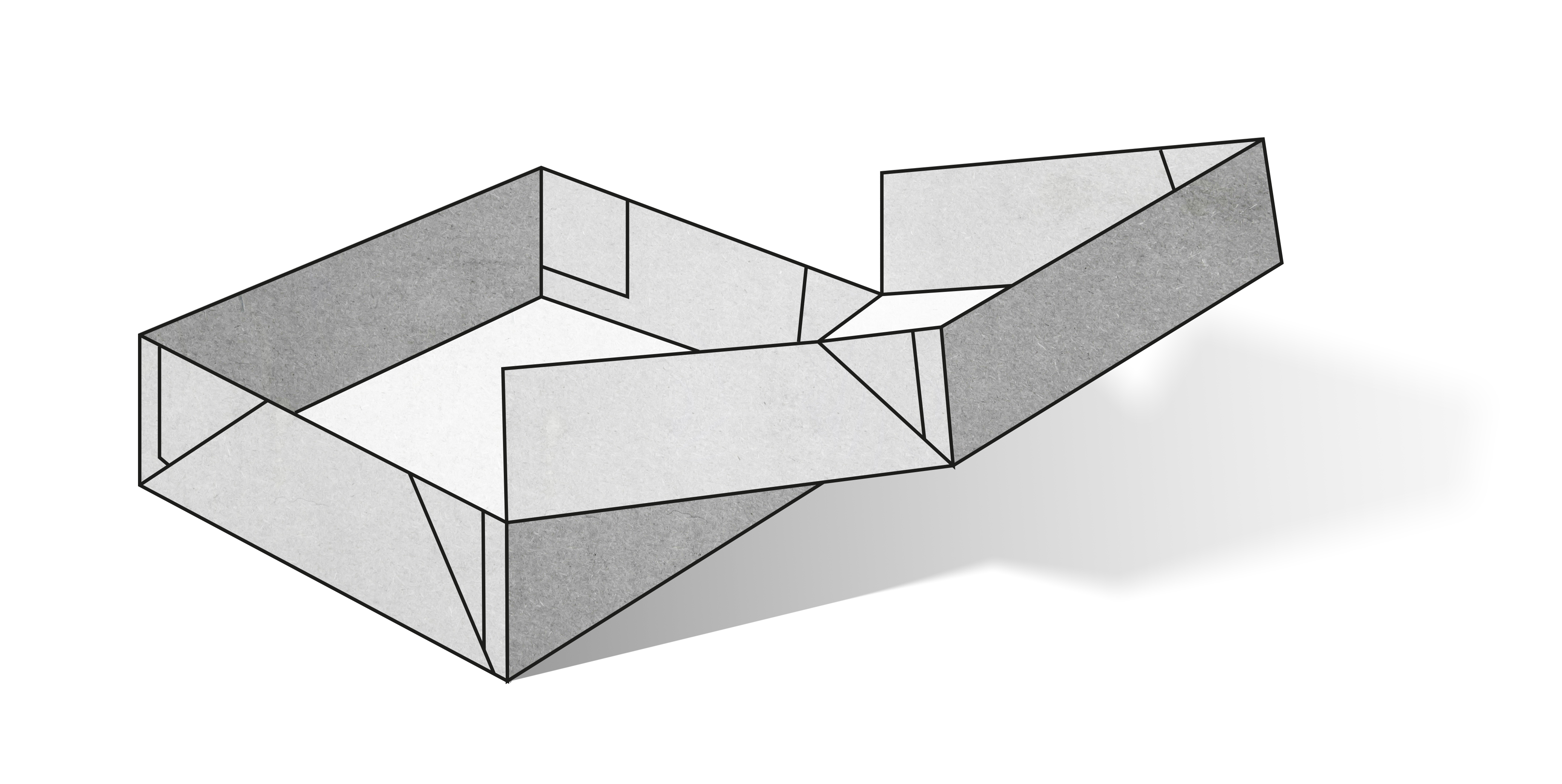
The CT 300 verifies standard colour codes and compact pharmaceutical codes!
- 100% verification to prevent product mix-ups
- Ensures maximum process reliability in folding carton production
- High optical resolution makes it possible to reduce code mark width by 50%
- Capable of monitoring colour on code marks measuring just 0.5mm
PX 1000 – The application head for precision gluing at maximum production speed!
- High closing force for minimal tailing and precision restart
- Reduced contamination means longer cleaning intervals and maximum productivity
- Processes a wide range of adhesive viscosities
- Maximum service life
- High process reliability in production
GDX 1000 – The optical sensor for monitoring glue nozzle application at maximum production speed!
- Monitors glue application 100%
- Monitors glue-free areas
- Integrated light barrier function for monitoring product length
- Sensor can be set up on the screen of the Xtend³ controller
Xcam – Monitors adhesive application and diagonal creasing!
Line scan cameras combined with UV or white LED linear lighting.
- Monitors adhesive application
- Detects glue-free areas
- Detects flaps
- Verifies diagonal creasing of the bottom flaps
The T&E module tracks products through the machine and automatically ejects them!
- 100% process reliability in production - functions on the fail-safe principle
- Ensures continuous production flows and maximum process reliability
- Capable of controlling all ejector types
Scan 300 – Laser scanner for detecting all common EAN codes!
- Examples: Code 128 / 2/5 Interleaved / Code 39
- 100% production control to prevent product mix-ups
Zur Anzeige des Klick-Modells nutzen Sie gerne unsere Desktop-Version.
Six-packs and special designs
Six-packs and other special designs put complex demands on gluing. For example, the adhesive may have to be applied by 16 or more application heads at several stations in a single folder-gluer.
High-tech folding mechanisms require precision dot application as well as monitoring equipment capable of reliably detecting even the smallest deviations. The Xcam camera equipment monitors all glue tracks and prevents the risk of inside gluing. Baumer hhs systems solve problems you have yet to encounter.
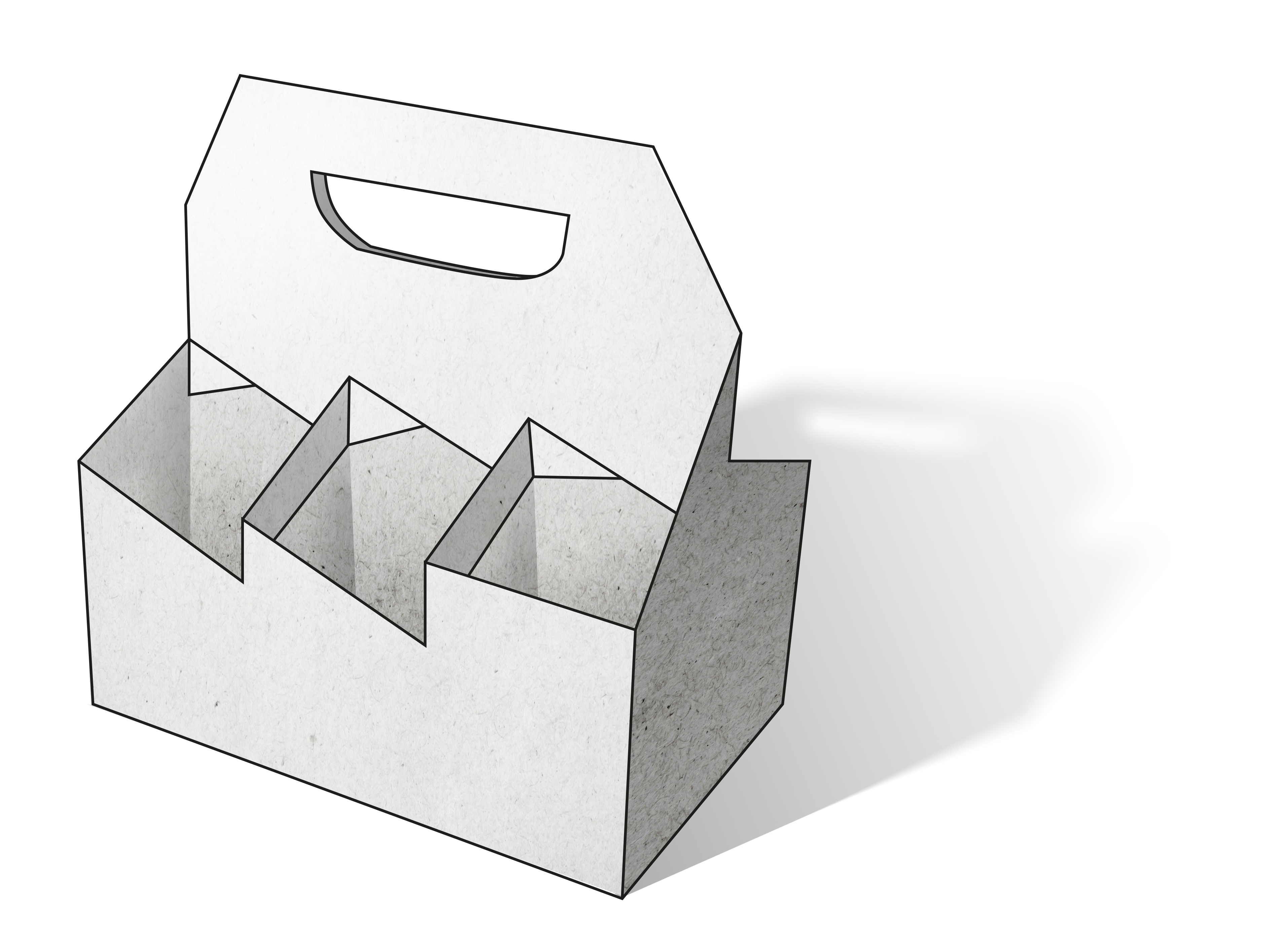
PX 1000 – The application head for precision gluing at maximum production speed!
- High closing force for minimal tailing and precision restart
- Reduced contamination means longer cleaning intervals and maximum productivity
- Processes a wide range of adhesive viscosities
- Maximum service life
- High process reliability in production
Scan 300 – Laser scanner for detecting all common EAN codes!
- Examples: Code 128 / 2/5 Interleaved / Code 39
- 100% production control to prevent product mix-ups
The T&E module tracks products through the machine and automatically ejects them!
- 100% process reliability in production - functions on the fail-safe principle
- Ensures continuous production flows and maximum process reliability
- Capable of controlling all ejector types
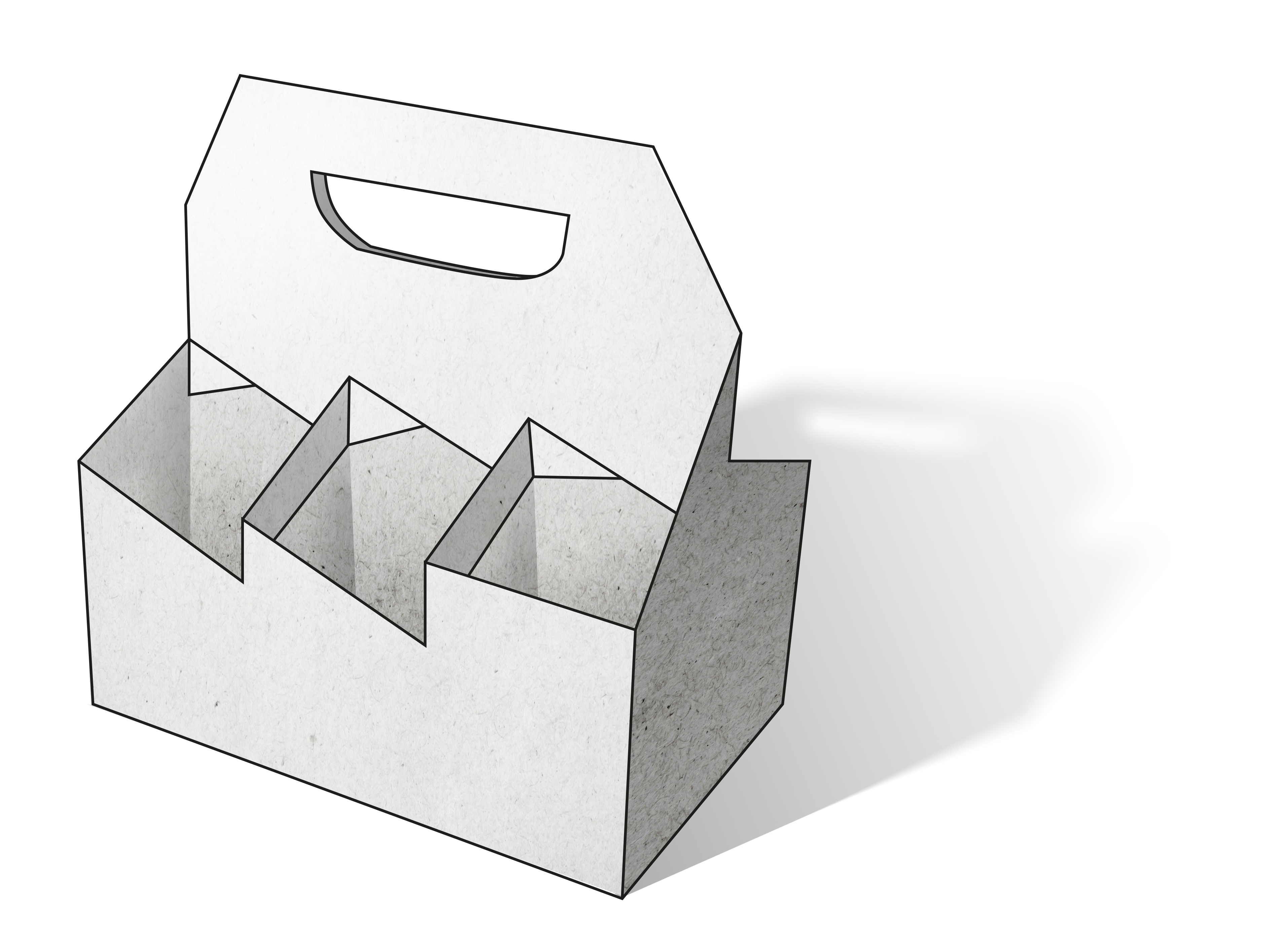
PX 1000 – The application head for precision gluing at maximum production speed!
- High closing force for minimal tailing and precision restart
- Reduced contamination means longer cleaning intervals and maximum productivity
- Processes a wide range of adhesive viscosities
- Maximum service life
- High process reliability in production
Scan 300 – Laser scanner for detecting all common EAN codes!
- Examples: Code 128 / 2/5 Interleaved / Code 39
- 100% production control to prevent product mix-ups
The T&E module tracks products through the machine and automatically ejects them!
- 100% process reliability in production - functions on the fail-safe principle
- Ensures continuous production flows and maximum process reliability
- Capable of controlling all ejector types
Zur Anzeige des Klick-Modells nutzen Sie gerne unsere Desktop-Version.
Side Seam Gluing Solution
Traditionally, in folding carton production the glue is applied to the glue flap with a wheel applicator. The problems associated with this process, such as cleaning and waste have been accepted by the industry for lack of alternatives.
Side Seam Gluing Solution from Baumer hhs now replaces existing disk gluing units and offers numerous associated advantages.
Xcheck DCM
The modern Xcheck DCM camera system monitors the feeder of the die cutter and thus closes an existing gap in quality monitoring. Inspection in the die cutter offers many advantages. For example, under-mixing of die-cut sheets is detected. The early detection of under-mixing in the process ensures less downtime and increases your productivity
- Simple integration
- Detection of 1D and 2D codes
- 100% quality control of all punched sheets
- For the front and back of the sheet
- Ready for future quality control requirements
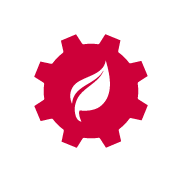
Sustainability
Resource-efficient for increased sustainability
Fast setup for perfect production startup
Minimises cleaning cycles
Reduces production downtime by means of quality assurance and product tracking
Dot application reduces glue consumption
Developed for greater reliability in production
Fail-safe principle
100% quality control
Perfect adhesive application
Production data networking and analysis
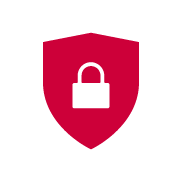
Reliability
Folding Carton Production - See for yourself!